Plastic extrusion for complex profiles and custom designs
Plastic extrusion for complex profiles and custom designs
Blog Article
A Comprehensive Overview to the Process and Benefits of Plastic Extrusion
In the large world of production, plastic extrusion emerges as a very reliable and essential process. Transmuting raw plastic into constant profiles, it provides to a wide variety of markets with its impressive flexibility.
Recognizing the Basics of Plastic Extrusion
While it may show up complex initially glimpse, the procedure of plastic extrusion is basically simple - plastic extrusion. It is a high-volume manufacturing technique in which raw plastic is melted and formed into a continuous account. The procedure starts with the feeding of plastic product, in the kind of granules, powders, or pellets, into a heated barrel. The plastic is after that thawed making use of a mix of warm and shear, applied by a rotating screw. Once the molten plastic reaches the end of the barrel, it is forced through a small opening referred to as a die, shaping it right into a wanted kind. The designed plastic is after that cooled, solidified, and cut right into preferred lengths, completing the procedure.
The Technical Refine of Plastic Extrusion Explained
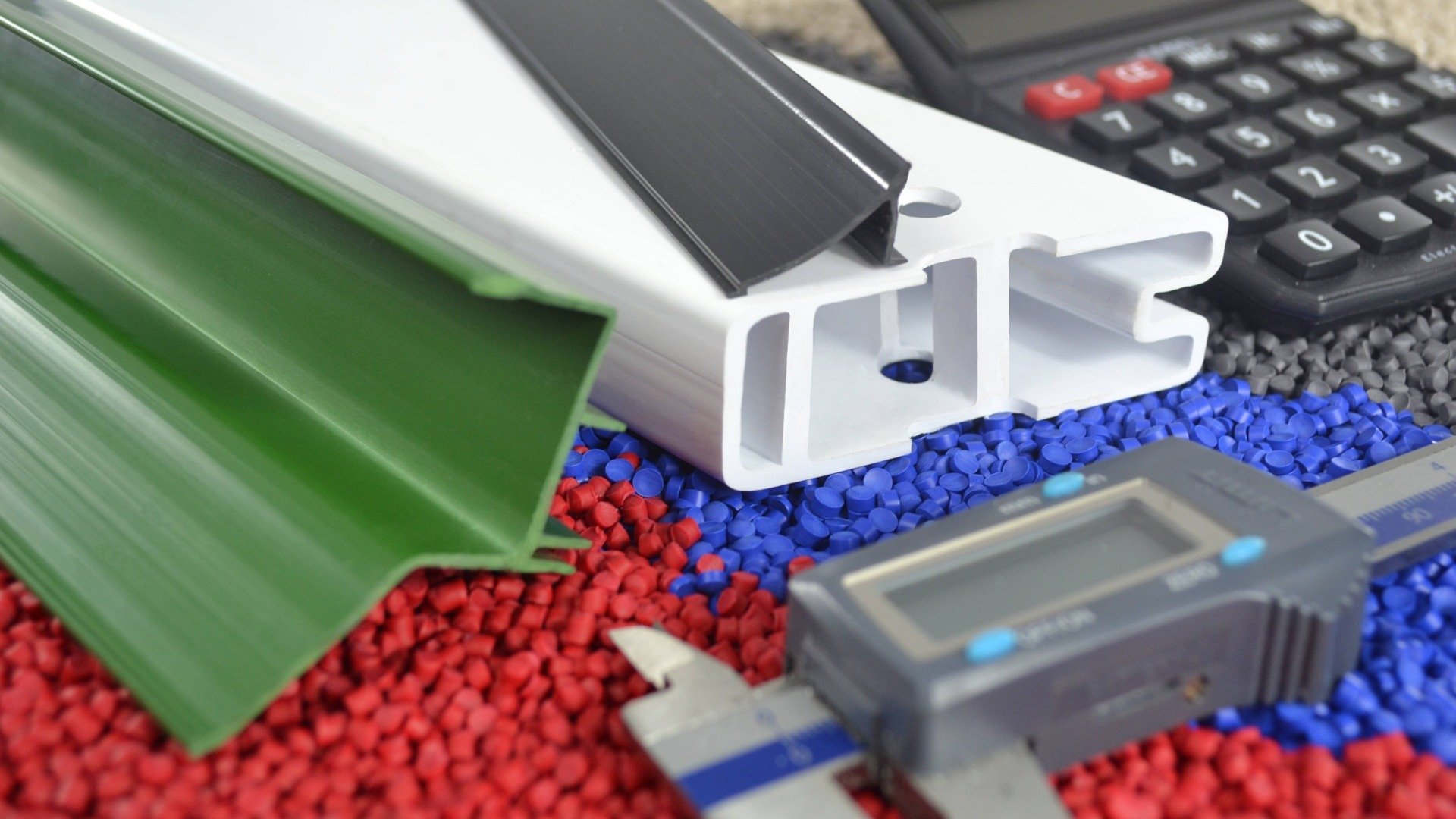
Kinds Of Plastic Suitable for Extrusion
The choice of the best type of plastic is a critical facet of the extrusion process. Various plastics use distinct residential properties, making them much more suited to certain applications. Comprehending these plastic types can significantly improve the extrusion procedure.
Contrasting Plastic Extrusion to Various Other Plastic Forming Techniques
Understanding the kinds of plastic ideal for extrusion leads the means for a more comprehensive conversation on exactly how plastic extrusion piles up against other plastic developing approaches. Plastic extrusion is unmatched when it comes to developing continual accounts, such as gaskets, seals, and pipelines. It additionally permits for a consistent cross-section along the size of the item.
Trick Benefits of Plastic Extrusion in Production
In the world of manufacturing, plastic extrusion offers many considerable advantages. One notable benefit is the cost-effectiveness of the procedure, that makes it an economically enticing manufacturing technique. In addition, this technique gives premium item adaptability and boosted manufacturing speed, thereby enhancing overall production effectiveness.
Cost-efficient Manufacturing Approach
Plastic extrusion leaps to the forefront as a cost-effective production technique in production. In addition, plastic extrusion calls for less energy than standard production approaches, contributing to reduced functional prices. In general, the financial advantages make plastic extrusion visit their website an extremely appealing alternative in the manufacturing sector.

Superior Product Versatility
Past the cost-effectiveness of plastic extrusion, another considerable advantage in producing lies in its superior product versatility. This makes plastic extrusion an optimal discover here solution for industries that call for customized plastic elements, such as vehicle, construction, and product packaging. In significance, plastic extrusion's product versatility promotes innovation while improving functional performance.
Boosted Manufacturing Speed
A substantial advantage of plastic extrusion exists in its enhanced production speed. This production procedure allows for high-volume production in a fairly short time span. It is qualified of generating long, continuous plastic profiles, which substantially decreases the manufacturing time. This high-speed manufacturing is specifically useful in markets where huge amounts of plastic parts are required within limited target dates. Couple of other production processes can match the rate of plastic extrusion. Additionally, the ability to preserve constant high-speed manufacturing without giving up item top quality establishes plastic extrusion apart from other methods. The boosted manufacturing rate, therefore, not only allows makers to fulfill high-demand orders however additionally adds to raised performance and cost-effectiveness. This useful function of plastic extrusion has actually made it a favored option in many industries.
Real-world Applications and Influences of Plastic Extrusion
In the realm of production, the strategy of plastic extrusion holds extensive importance. The financial advantage of plastic extrusion, mainly its high-volume and affordable result, has actually transformed manufacturing. The sector is constantly aiming for developments in recyclable and eco-friendly products, navigate here indicating a future where the advantages of plastic extrusion can be retained without compromising environmental sustainability.
Conclusion
In final thought, plastic extrusion is a extremely effective and efficient method of changing raw products into diverse products. It supplies countless advantages over various other plastic developing approaches, consisting of cost-effectiveness, high result, very little waste, and design flexibility. Its effect is exceptionally felt in various industries such as building, automobile, and consumer goods, making it a pivotal process in today's manufacturing landscape.
Diving much deeper into the technical process of plastic extrusion, it starts with the selection of the proper plastic product. Once cooled, the plastic is reduced right into the needed lengths or injury onto reels if the item is a plastic movie or sheet - plastic extrusion. Comparing Plastic Extrusion to Other Plastic Forming Approaches
Understanding the types of plastic appropriate for extrusion paves the method for a broader discussion on just how plastic extrusion stacks up against various other plastic creating approaches. Few various other manufacturing procedures can match the speed of plastic extrusion.
Report this page